Return Workflow for Warehouse
The return workflow in the warehouse aims to ensure the accurate processing of returned items, maintaining inventory integrity and providing clear documentation for future reference. This process is managed by the Operations Team, who is responsible for overseeing the verification and recording of returned items upon their arrival.
- Role and Responsibility: The Operations Team in the warehouse is tasked with the management of returned items, ensuring they are accurately recorded and processed.
- Timing: The workflow initiates upon the delivery of return items to the warehouse.
- Task Overview: The main task involves verifying the return items and creating purchase orders for inbound waste items.
- Steps:
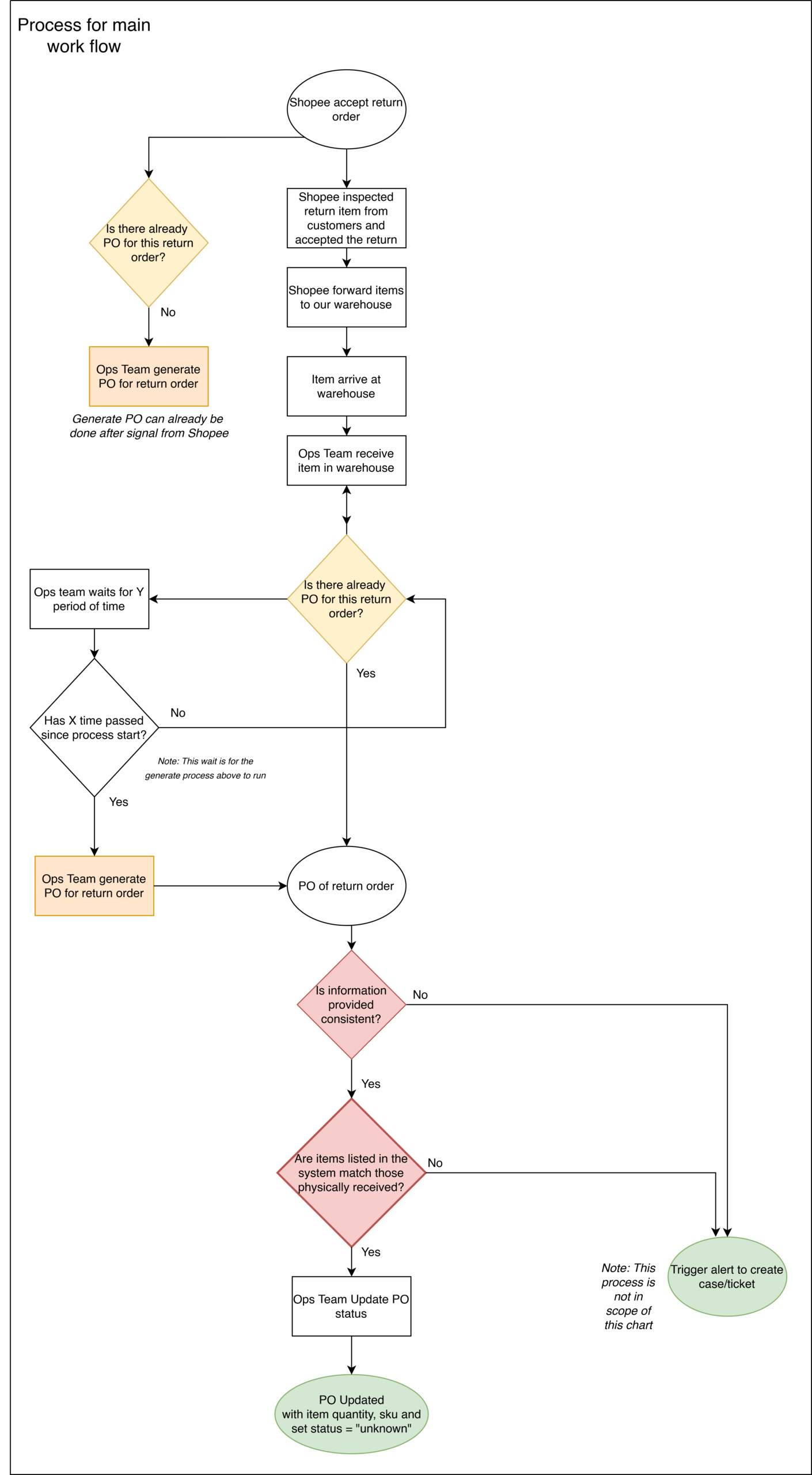
- Shopee return accept
- Create Purchase Order: Ops team check if a purchase order corresponding to the return order has been automatically created. If no wait Y time and rẹcheck. After a total X time, a purchase order is then created for the received items. This order includes the order ID, return ID, items received, quantities, condition, and receipt date.
- User send product back to warehouse
- Product arrive at warehouse
- Repeat step 2
- Cross-Reference IDs: The Operations Team first cross-references the received items with the system. This step ensures that the items shipped align with those received. If the process is automated, the Ops Team only needs to cross-ref from PO.
- Verify Items: The next step is to verify that the items listed in the system match those received. The status of item is unknown (Another process will check the condition)
- Update System: Finally, the warehouse management system is updated with the new purchase order details and any documented discrepancies. This ensures that inventory records are accurate and up-to-date, facilitating efficient warehouse operations.
Note: cross reference:
- priority is External order Code
- sub-priority is inside note portion